
TAKING A HARD LINE ON PLUMBING
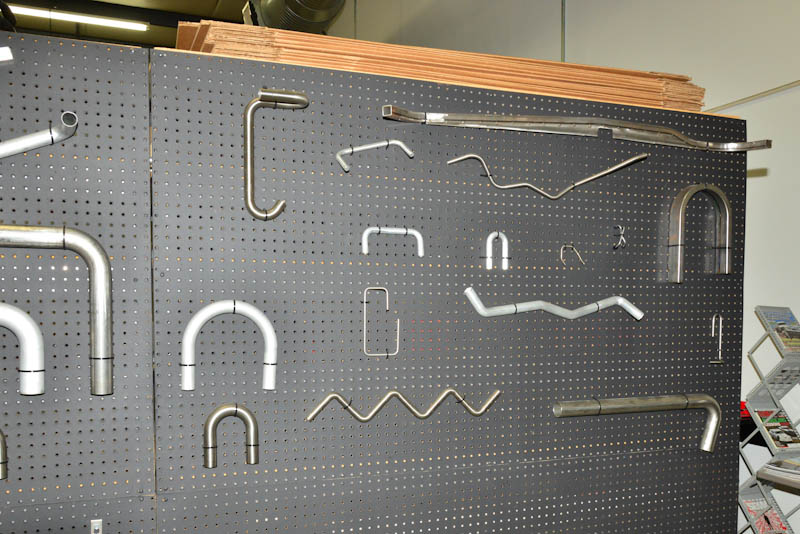
When most people think of fluid lines, flexible hose usually comes into mind. Fuel, oil and even brake fluid can be carried adequately through hosing. However, there are many areas where steel or aluminum tubing does a better and safer job.
Obviously we use long runs of steel tubing to carry brake fluid because of the pressure utilized, as hosing has a tendency to swell. Naturally small runs of flexible hose are necessary in brake systems but they should be kept as short as possible. And of course there are many other areas where flexible hosing is used but steel or aluminum lines sometimes offers a better and safer alternative. However, bending tubing to fit along with adding fittings on the end can sometimes cause more headaches than they’re worth. Having the proper equipment is a necessary first.
“We got into the tube bending business years ago when NASCAR wanted to get away from having oil lines run inside the driver’s compartment,” says John Harper of Brown & Miller Racing Solutions.
Most noted for their hose and fitting manufacturing capabilities, Brown & Miller took a long hard look as to what was available in the way of bending and manufacturing steel and aluminum lines and decided to jump head first into the business, making a considerable investment in machines and tooling to bend and fabricate hard lines.
Located in Concord, North Carolina, the heart of stock car racing, Brown & Miller’s business centered around the circle track business. But sharp drag racers soon found Brown & Miller’s expertise in the area of hoses; and in recent years wiring; to be the perfect venue for quality components. That business now extends to the hard lines which Brown & Miller have now also been famous for.
“We can bend anything from small 1/8-inch tubing right up to two-inch diameter,” says Harper. “Not only is the tubing used for fluid, but we also bend up roll cage material for a couple of sprint car manufacturers. Basically we supply them with every bent tube in the car. All they have to do is notch the tubing where required and they’re ready to weld a frame together. Of course, they can bend it all themselves, but from a standardization standpoint, it’s more cost-effective to have us do it. In addition, because of the CNC bending equipment we have, we can hold tolerances of the bends to just a couple of thousandths of an inch.”
An example of their capabilities are the injector lines used by many of the nitro teams. In the case of blower explosions, in addition to the many other parts destroyed, so too are the hard injector lines. “A lot of those teams will send us a sample line, which we’ll measure and duplicate,” says Harper. “We can then supply them with as many spares as they’d like in addition to us keeping the line specifics on file so that when they need more, we simply pull the file up on the computer, output it to the bender and bend as many more as they need in addition to adding the necessary fittings.”
Besides the CNC bending equipment, Brown & Miller uses sophisticated CMM measuring equipment to ensure that each tube is bent to the correct specs.
One of the biggest concerns these days is fluid leaks onto the racing surface. Besides causing a clean-up problem in itself, it can also be a dangerous situation. Gone are the days (or they should be) where rubber hose and clamps are all that’s necessary to move fluid. Each hose used on a race car should have a solid connection; all in the name of safety.
SOURCE
Brown & Miller Racing Solutions
704.793.4319
www.bmrsusa.com