
BALANCING ACT
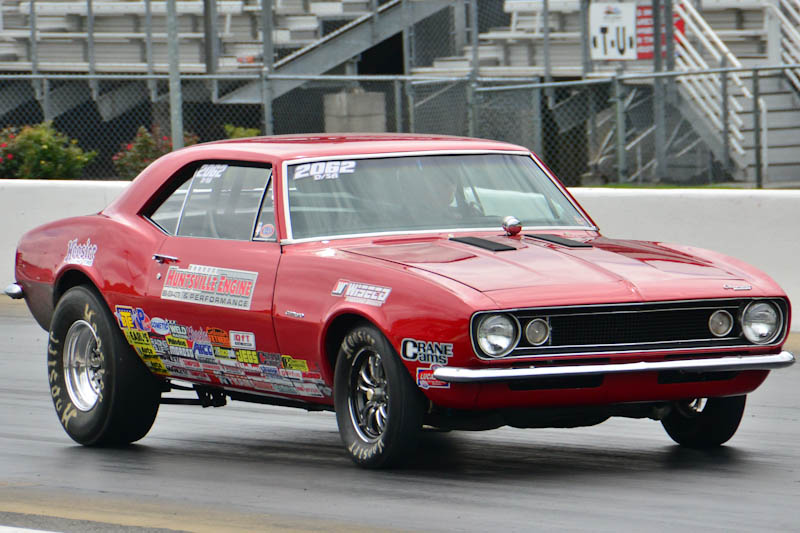
Brake Light Racing Requires a Balanced Brake System
(This story first appeared in 2017 but is still relevant today. -ed.)
Brake light racing is getting a bad name. Oh, it maybe never really had any kind of a “name,” instead just
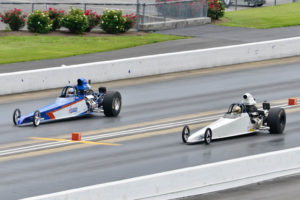
Anytime there is an index or dial-in placed on a car, you run the risk of the driver having to use the brake pedal to avoid breaking out which can lead to excessive braking.
a… name. There have been certain times when a racer was disqualified from competition for excessive braking and we’re not going to debate whether or not that decision was right or wrong, but question as to just how does one stop “excessive braking.”
A little DISCLAIMER first: Following any of the suggestions we make here WILL NOT guarantee you won’t lock-up the brakes at the finish line, nor be exempt from becoming another victim of a disqualification. Becoming victim to that rule is really only minor in the general scheme of damage you can incur to both your car and your body, making only common sense a way to alleviate both.
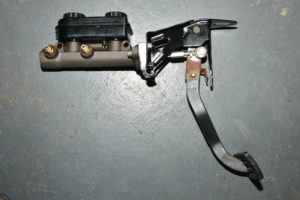
It all begins with the choice of master cylinder and pedal leverage ratio.
Bear in mind that excessive braking is a natural result of the rules we play with. We’ve said this before, but anytime you place a dial-in or index on a car and get the Lose ticket when you run under that dial, you create the natural tendency to use the brakes well before the finish line to avoid breaking out. While touching the brake pedal slightly might be necessary, excessive braking is a whole other topic.
The NHRA Rulebook is pretty clear on this: “Anytime it has been judged that excessive braking has resulted in loss of control that results in contact with the guardwall and/or light fixtures or crossing the center boundary lines, INCLUDING PAST THE FINISH LINE, the contestant will be disqualified.”
Naturally, hitting anything or crossing the boundary lines, would be deemed to be excessive braking by

For most conditions, 1,000psi of pressure is required to fully lock-up calipers. The use of a pressure such as this Strange Engineering unit will assure you have that amount.
officials, including skid marks and/or front end dipping hard. All of which makes the ruling rather subjective, but how does one stop from locking up the brakes and causing skid marks and/or getting the front end not to dip?
As far as the aforementioned second item is concerned, dipping is something you’re never going to stop and if you’re a door car racer, it’s just part of the game. “Dipping” of the front end happens automatically when the brakes are applied even lightly. Dragsters are less susceptible to notice dipping of the front end as most have no front-end travel. In that instance, it’s harder to determine excessive braking. Tim Irwin of Moser Engineering once said, “You watch a Super Comp car at the finish line versus a Stocker and you’d think the Stocker was jamming the brakes a lot harder than the dragster because of the travel in the front suspension.”
Stock bodied vehicles need a loose front end travel to transfer weight on the starting line. However, this causes the front end to drop hard at the finish line when the driver even hits the brakes a little.
The first step in a proper brake system begins with pedal ratio. That is the distance from the pedal to the pedal’s pivot mount divided by the pivot to the master cylinder pushrod. In most cases a six or seven to one ratio is required to adequately supply enough fluid pressure to the calipers in order to stop the car.
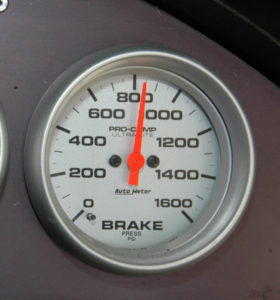
While 1,000psi will sufficiently lock up your brake calipers, under most race conditions, you’ll rarely see pressures over 600-800.
Brake pressure is developed by the force applied to the pedal, leverage ratio, and master cylinder bore size. When it comes to a four-wheel disc brake system with four calipers, a recommendation of 5-1/4 to 5-1/2 to 1 ratio with a 1.032” bore master cylinder, and 6-1/4 to 6-1/2 ratio with a 1.125” bore. This is when using disc brakes, as drum brakes require less pressure. Strange Engineering also makes a stepped bore two-stage master cylinder. One for a dragster and one for a door car. They utilize a large bore to deliver the volume of fluid, and a small bore to develop pressure.
More ratio and the pedal becomes very touchy in that more fluid pressure will be fed to the calipers causing them to lock-up easier. Less ratio and you’d have to press harder on the pedal to get the car to stop. It’s kind of a Catch 22 in that too much is not good and neither is too little, making the first step in the design of the proper brake system to be pedal ratio.
Oftentimes in the case of our circle track cousins on the NASCAR circuit, they’ll design the brake system to suit the driver. Where typically a -3 hose is used to plumb the calipers, there are instances where a smaller -2 line will be used to create a better feel for the driver.
Volume and pressure also play a big part in stopping a car. In the past, car builders used Chrysler-style master cylinders in their race car builds. They were aluminum bodies with plastic reservoirs which made them attractive to use because of their light weight. These cylinders were designed to be used on power assist brake systems or a car with a pedal ratio of 7 to 1 or higher. Several companies have designed master cylinders with as small as 7/8” bores which should only be used on cars such as dragsters with two rear brake calipers. The smaller bore allows for the required pressure but because there are only two calipers to operate, they require less volume. This makes master cylinder bore size extremely important.
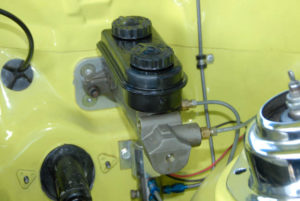
The standard issue Chrysler-style dual master cylinder is available in two different bore sizes. The use of the proper bore size for your application is imperative.
The use of the correct bore size master is as important as pressure itself. Both volume and pressure work hand-in-hand. As in any hydraulic system, you can have pressure and no volume or vice-versa. As Irwin asserted, a 7/8” bore master is sufficient on a dragster because there are typically only two brake calipers to fill. For that same reason, on a full-bodied vehicle with four calipers, there is a need for a larger bore master, i.e. more volume.
In the case of a four-wheel system, a master cylinder with an 1-1/8” bore should be sufficient when coupled with a 6:1 pedal ratio. What you’re aiming for is around 1,000psi of brake fluid pressure to the rear calipers. Although, that number would be achieved with a lot of foot effort since that would only be necessary for full lock-up of the wheels. The actual pressure required under normal stopping conditions would therefore be less.
“Front to rear brake bias is of great importance when it comes to four-wheel brake systems,” said Strange Engineering’s Jeff Stange.
Oftentimes a proportioning valve will be used to reduce pressure to the front or rear. “We actually suggest the use of a proportioning valve to reduce front brake pressure,” says Stange. “This is based on the assumption that on a drag race car, the rear slicks will have a larger contact patch on the ground than fronts.”
Still, in most cases you certainly don’t want the front brakes locking up before the rear. Because front tires have less of a contact patch on the ground than do rear slicks, they can easily be locked up providing for the same brake pressure as the rear. Oftentimes then a proportioning valve will be used to reduce front brake pressure. While the 1,000psi number is sufficient for the rear, somewhere in the neighborhood of 600psi is all the fronts require.
It’s also important now to mention the use of a residual pressure valve which is not much more than a one-way valve. This is used to maintain a certain amount of fluid in the calipers when the master is mounted at or below the level of the calipers. In this case, a 2-lb. valve is used which will keep the fluid from bleeding back to the master cylinder, but not cause brake drag. This is common for dragsters.
Irwin also had an interesting thought when it came to tubing size. “We should take from hydraulic specialists in that long plumbing runs benefit from bigger diameter lines. All passenger cars built, even early designs use 1/4” lines to the rear to aid in fluid flow in long runs. Most current race car plumbing kits use 3/16’ lines to the rear. However, the small line restricts the fluid return to the master cylinder which causes slow release times on the rear brakes. This can be especially beneficial to foot-brake cars.”
What this comes down to is that it is essentially important to measure the amount of pressure you have going to the fronts and rears, or just rears in the case of dragsters, of your brake system once it’s installed. This can very easily be accomplished with the use of a brake pressure gauge such as the one from Strange Engineering which screws directly into the bleeder screw port of the calipers.
In any event, the proper set-up of your brake system is as important as any other components of your race car.
SOURCE
Moser Engineering
260.726.6689
www.moserengineering.com
Strange Engineering
847.663.1701
www.strangeengineering.net